The Challenges of High-Mix Tube Fabricators
Media 2021/07/26
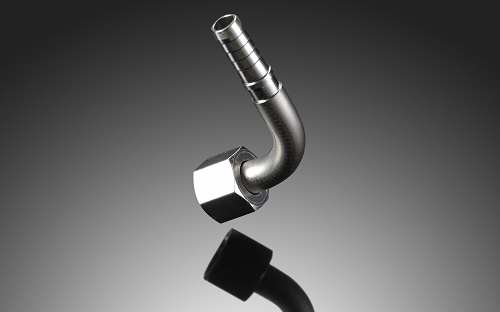
Companies like AG make a large variety of products in small quantities in response to numerous orders placed by their customers. As an example, AG counts over 4,500 different production codes, and each code corresponds to an average batch of less than 40 workpieces. The constant need to produce parts in great variety and small batches with very tight delivery times often challenges fabricators, which have to accept specification changes while still respecting deadlines.
As high-mix/low-volume manufacturers want to be highly responsive to the introduction of new products, they need to optimize and control the production process at all levels. Only a comprehensive vision of the production and equipment operating status in real-time will allow the fabricator to make changes efficiently.
How is Control Possible?
In 2012, AG decided to purchase SOCO's machines. They were initially installed in the Italian headquarters. Then, as they proved to be a game-changer for the manufacturer, they were installed in other factories of the group. The flexibility of SOCO's machines and their interconnectivity have been essential for AG's production activities.
Currently, AG has a complete mix of SOCO products that are interconnected, starting from Tube Cutting and End Finishing, to Washing and Laser Marking, as well as complete Tube Bending Automation Cells.
Creating new parts, making tool changes, and recalling old parts are all actions that require clean and accurate data input-output. Precise data collection was only possible with high levels of automation and instant feedback from the production floor. SOCO's intelligent machines, fully automated solutions, with an easy setup and powerful control software, were a complete solution unlike any others in the market.
1. Easily Input Data and Design with i2 Controls
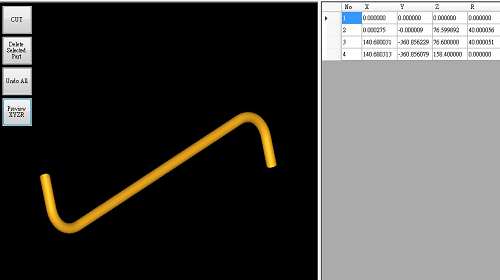
Once the tooling information is inserted, the software gives a 3D model preview of the tube and the bending process, suggesting changes in case of collisions. The i2 Controls also unbends the model to determine the raw material length: this means that there is minimal waste of material in the production. The software, through its various types of simulation and speed optimization, assures high performance and accuracy when making new parts, and it helps in reverse-engineering existing parts as well.
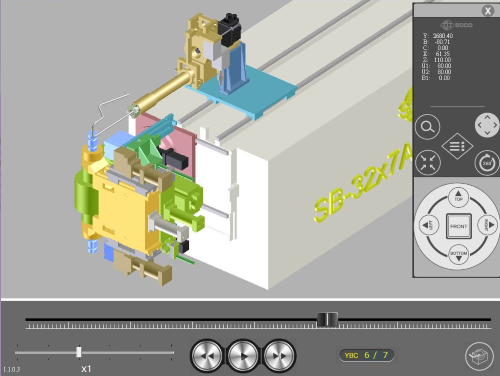
2. Precise Measuring Systems
The i2 software connects SOCO's Tube bending machines with Coordinate Measuring Machines (CMMs). The CMM measuring systems are networked directly to SOCO's CNC tube benders to ensure tube bends are produced to the highest possible standard. Once the measuring system computes the bent tube, it sends the data directly to the tube bending machine, automating the corrections loop. This process improves accuracy, eliminates data entry mistakes, and increases production for the tube fabricator, with no prototyping, waste, or re-work.
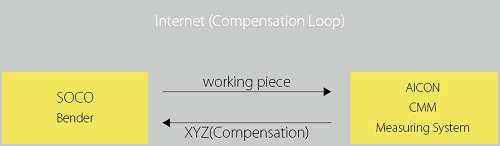
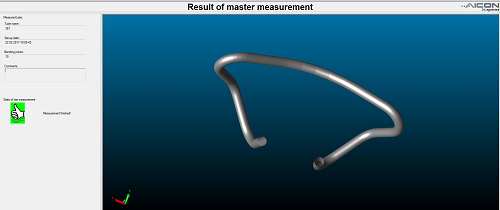
3. IRMS: From Production Reports to Service and Maintenance
The i2 Reports and User Permissions Controls also provide the fabricator with detailed production reports of outputs by time frame, operator, and machine. Depending on the authorization level, users have various types of access such as file creation, view, editing, and troubleshooting.
The i2 Maintenance System allows full customization of alarms for daily, weekly, quarterly, or yearly checkups. In case of stoppage, messages will be displayed on the screen and the system will keep a complete log of service records. Finally, it is also possible to get in touch with SOCO's after-sales engineers and service support through live, on-screen troubleshooting.
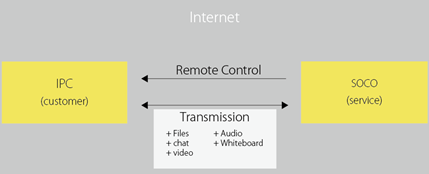
The Advantages of Smart Manufacturing
The high-mix/low-volume model makes it necessary for a factory to have full control and real-time feedback over its production. As more and more shops produce small volumes of increasingly customized parts, they need versatile and multi-tasking machines equipped with advanced functions to handle a greater number of applications.
Thanks to the flexibility and intuitiveness of SOCO's manufacturing solutions, high-diversity factories can quickly and efficiently switch between a variety of jobs and expand to different industries. The interconnection capabilities allow remote control over the production, and project updates become quick and reliable. Smart manufacturing solutions like SOCO's i2 Controls allow customers to generate maximum value, assuring that all the elements of the manufacturing process are precise and reliable.
